In der Bremsentechnik für PKWs und LKWs spielt in der Entwicklungsphase die Erfassung des Verschleißes von Bremsbelägen eine große Rolle. Deshalb muss die Vermessung der Beläge möglichst genau und mit geringem Zeitaufwand erfolgen. Eine automatische optische Vermessung der Bremsbeläge hat gegenüber der manuellen Vermessung einige Vorteile.
Manuelle Messung
Bremsbeläge werden in der Entwicklungsphase diversen Tests unterzogen, und anschließend der Verschleiß bestimmt, um daraus die zu erwartende achs- und fahrzeugspezifische Gesamtlebensdauer zu berechnen. Üblicherweise wird dafür an mehreren Stellen die Dicke des gesamten Bremsbelags bestehend aus der Rückenplatte und dem Belag-Material gemessen. Diese Vermessung wird bisher mit einer Mikrometerschraube durchgeführt. Je nach Anlegen der Bügelmessschraube können die Werte von Bediener zu Bediener variieren.
Aus den Messpunkten wird zusätzlich der tangentiale und der radiale Schrägverschleiß bestimmt. Pro Achse müssen hier 16 bzw. 32 Messungen durchgeführt werden. Folgende Abbildung zeigt ein schematisches Bild eines Bremsbelags mit vier Messpositionen.
Abbildung 1: Schematische Darstellung eines Bremsbelags mit vier Messpositionen
Automatische Vermessung
Die automatische optische Vermessung der Bremsbeläge bedient sich der Laser-Triangulationstechnik. Hierzu wird eine Laserlinie auf den Belag projiziert und deren Abbildung mit einer in einem Winkel dazu ausgerichteten Kamera aufgenommen. Genaueres zu diesem Verfahren können Sie in unserem Blogbeitrag 3D-Sensoren für die automatische optische Inspektion (Teil 1) nachlesen.
Um die tatsächliche Belagdicke zu ermitteln, wird neben der Belagoberfläche auch die Position der Rückenplatte erfasst. Da die Rückenplatte seitlich nur wenig über das Belagmaterial übersteht, kann diese allerdings in diesem Bereich mit herkömmlichen Laserscannern nicht erfasst werden. in-situ hat deshalb das Verfahren weiterentwickelt und setzt auf eine rotatorische Abtastung des Bremsbelags. Mit diesem Rotationsscanner können alle relevanten Bereiche auf der Oberfläche sicher erfasst werden.
Abbildung 2: Schematische Darstellung des Rotationsscanners
Für die automatische Vermessung wird der Bremsbelag auf einer Drehplatte positioniert. Da sich an der Unterseite der Bremsbeläge noch Klammern oder Metallfedern befinden können, besteht die Auflage aus zwei Zylindern, deren Position an verschiedene Belag-Größen angepasst werden kann. Um ein Verrutschen der Beläge während der Drehung beim Scan-Vorgang zu verhindern, ist in den Zylindern ein Magnet eingesetzt, der die Beläge fixiert.
Abbildung 3: Positionierung des Bremsbelags in der Messkammer
Das Ergebnis des Scans ist eine 3D-Punktewolke, wie diese in Abbildung 4 dargestellt ist. Zur Auswertung der Messung werden zwei Ebenen (Rückenplatte und Belag-Material) ermittelt, wobei sogenannte „Ausreißer“ ignoriert werden. Diese können durch Schmutzpartikel, Poren oder Ausbrüche hervorgerufen werden. Zur Bestimmung der Ausreißer wird ein Relaxationsalgorithmus eingesetzt. Die Differenz beider Ebenen an den definierten Messpunkten ergibt die zu messende Belagdicke. Aus diesen Messdaten können nun Rückschlüsse auf den tangentialen und radialen Schrägverschleiß gezogen werden.
Abbildung 4: Punktewolke eines Bremsbelags
Der Scanvorgang eines Bremsbelags dauert etwa 1-2 s. Anschließend stehen die Messdaten in der Software zur Verfügung und werden automatisch zu zuvor angelegte Achs-Konfigurationen hinzugefügt. So ist jederzeit ein Zugriff auf die historischen Daten möglich. Auf diese Weise sind Übertragungsfehler, wie sie bei der manuellen Messung vorkommen können, ausgeschlossen.
Vorteile
- Bedienerunabhängige Messung, da kein manuelles Anlegen der Mikrometerschraube nötig ist.
- Schnelle Messung aller Messpunkte auf einem Belag. Während des Scans kann zudem der nächste Bremsbelag bereits vorbereitet werden.
- Exakte Bestimmung der Oberkante der Rückenplatte und exakte Erfassung der tatsächlichen Bremsbelagdicke.
- Tolerant gegen Oberflächen-Störungen wie Ausbrüche und Poren.
- Keine Übertragungsfehler möglich wie bei manuellen Messsystemen.
- Automatische Zuordnung der Messdaten zu Achs-Konfigurationen um historische Messfolgen abzubilden.
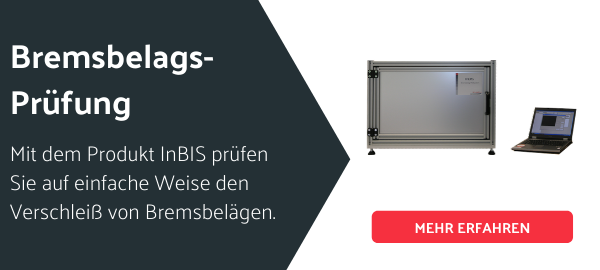